Delphi YDT840 Hydraulic Diagnostic Tester
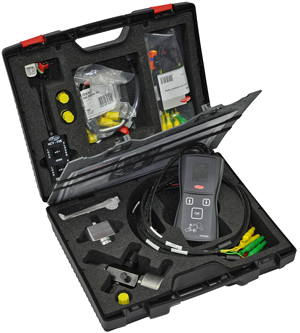
Delphi YDT840 Hydraulic Diagnostic Tester
Delphi presents a new hydraulic diagnostic package which is specifically dedicated to Diesel specialists and workshops, taking them to the next level of diagnostics expertise.
Specifically designed to be compatible with Light Duty, Medium Duty and Heavy Duty Common Rail and GDI systems and to complement and enhance the current YDT860 H3PI Hydraulic Diagnostic tooling, the HD3000 bridges the gap in current tooling capability. An innovative response to complicated diagnostics of automotive high pressure, it combines safety and flexibility within a “first to market”, patented design.
Product Description
The HD3000 is a complete hydraulic diagnostic tool kit that allows a deep analysis of the high pressure issues on the Fuel Injection Equipment technology of all modern vehicles. It is compatible with Diesel & GDI technologies and covers light-duty, medium-duty and heavy-duty applications.
The kit is composed of the key mechanical and electrical devices capable of confirming a high pressure fault. By measuring the system pressure in the Static and Dynamic modes, faults with injector pressure drift and excessive back leak flow can be determined. In addition, faults within the pump, the pressure sensor or the high pressure valve can also be detected.
The tool is capable of testing systems by setting and precisely controlling pressures up to 3000bar. It is complemented by a cleaning device aimed at removing any lacquering from the inlet valves of High Pressure pumps to get them back to their original specification.
Thanks to its wide flexibility, the Delphi HD3000 incorporates several tools in one, allowing the user to safely set any pressure test condition on the engine and consequently detect malfunctions which no other tool in the market can see. Its unique combination of testing functionalities allows it to set the engine in operating limit conditions for deep analysis of the performance of the Fuel Injection System.
Features and Benefits
With the ability to perform dedicated test routines on a number of the key components within the Fuel Injection Equipment, the Technician can check the operation of the Common Rail system by controlling actuators such as the IMV or the HPV and finally clean all types of Delphi IMV – all with one tool and eight simple test routines.
Functional Tests
The simple, functional tests include -
- Pump capacity test under cranking – check the ability of the pump to create pressure under cranking.
- Pump capacity routine test for Delphi Applications – for this test, the use of an OBD diagnostic tool will also be required to check if the vehicle has a “pump capacity check” routine within the diagnostic software. By creating an injection system leak for a given pressure, this mode allows the check of the capacity of the pump to generate both the requested pressure and flow using the diagnostic routine.
- Pump capacity test without routine for All Makes – this mode is for both Delphi and All Makes applications without a predefined routine in the engine ECU. This can test the pump’s capacity to generate pressure at idle by manually controlling the vehicle actuators.
- Injector return flow under load at idle – to check the operation of the injectors under load (pump capacity requirement) at idle.
- HPV leak test – allows the operation of the HPV to be tested by manual control.
- IMV cleaning – this simple procedure will allow the removal of lacquering from the IMV. The addition of solvent cleaner (part number 9001-908) will be required for this function along with the YDT846 IMV cleaning assembly supplied within the kit
Additional Tests
- Delphi heavy duty systems – capable of measuring peak pressure during cranking on F2E systems, plus cranking and running pressure on EUP systems.
- Heavy Duty Common Rail systems – capable of performing same tests as light duty up to 3000bar.
- GDI systems – with the specific GDI adapters supplied within the kit, it has the capability to measure the natural cranking pressure.
- As the HD3000 is fitted with a pressure sensor, you can also use it to check for any drift of the electrical characteristics of the pressure sensor fitted on the engine rail. The values can be compared directly with those measured by the HD3000 pressure sensor when connected to the high pressure system.
Safety Requirements
It is advisable that users of the YDT840 take reasonable precautions to maintain a safe working environment.
Any intervention on the Common Rail injection systems must be carried out by qualified personnel using appropriate Tooling.
- Before installing the equipment, ensure the ignition is switched off and the key is removed.
- Take the necessary precautions concerning mechanical and electrical safety.
- DO NOT carry out any intervention on the Common Rail injection system with the engine running.
- DO NOT carry out any work on the fuel circuit until rail pressure and fuel temperature readings have been taken using the diagnostic tool. You can only begin to open fuel circuits when the fuel temperature is lower than 50 °C and the rail pressure is close to 0 Bar. If communication with the DCU is not possible, leave sufficient time before commencing work on the fuel circuit.
- DO NOT electrically disconnect any system component when the engine is running.
- DO NOT disconnect the vehicle battery when the engine Is running. Always follow the correct procedure when disconnecting and re-connecting the vehicle battery.
User Requirements
It is imperative that the YDT840 is only operated by Common Rail Fuel Injection equipment trained technicians, who have completed the appropriate Training Courses and gained a full and comprehensive understanding of this type of system. Contact your Authorised Delphi Distributor for further details regarding available training.